Sim, você leu certo. A primeira palavra do título remete as principais questões abordadas para justificar a ACR: $ -> Dinheiro e T -> Tempo.
Aproveitando para reforçar, análise de causa raiz segundo Uberoi et al. (2004), tem como objetivo descobrir o que ocorreu, porquê ocorreu e o que fazer para prevenir a recorrência do problema.
Então vamos começar pela questão tempo. Seguido ouvimos dizer que não têm tempo para fazer a ACR porque já estão assoberbados de tarefas. Normalmente quem diz isso está ligado diretamente a operação e tende a ter uma cultura reativa.
Também escutamos que ACR é muito cara, pois necessita de várias horas de pessoas competentes e treinadas. Essa costuma ser uma perspectiva das pessoas mais afastadas da operação. É fácil verificar isso em perguntas do tipo “Quanto isso vai custar?” ao invés de “Que valor isso vai trazer para a empresa?”.
Então, vamos avançar para verificar porque superar esses paradigmas.
Será que não temos tempo para ACR?
Tempo é um dos bens mais preciosos que temos, é o que chamamos recurso escasso. E por isso deve ser bem aproveitado. Nós não achamos que a ACR vai resolver completamente essa questão. Acreditamos que a ACR pode lhe ajudar a perder menos tempo com problema reincidentes, e com isso poderá utilizar melhor o seu tempo em atividades que agregam mais valor ao seu dia a dia. Outro grande benefício destes momentos é a experiência que o time adquire, ganhando assim tempo na formação da equipe.
Supondo que no seu diário de bordo, ou controle de atividades, esteja relatado (manual ou automaticamente) perda de 15% por problemas conhecidos que volta e meia retornam para lhe assombrar. Essa perda pode ser uma máquina que deixou de trabalhar por 3,6 horas diárias porque quebrou ou porque produziu produtos defeituosos no período.
Agora imagine se você ganhasse esse tempo todos os dias. Legal né? Essa deve ser a busca para aumentar a competitividade. Várias empresas de ponta estão conseguindo ótimos resultados e você pode melhorar muito também. Mas para isso é necessário afinco de várias áreas integradas buscando eliminar a causa raiz dos problemas.
Já dizem os filósofos populares “Errar uma vez tudo bem, agora cometer o mesmo erro várias vezes já é burrice”.
Será a ACR muito cara?
Se tempo é dinheiro, então é melhor não jogar nenhum dos dois pelo ralo. Então vou ajudar você a entender melhor a integração desses pensamentos, e também para fundamentar a defesa da ACR. Se uma máquina quebrar por uma falha mecânica, existe o custo da peça a ser substituída e da mão de obra. Correto? Isso é o que a maioria das pessoas pensam. Avançando um pouco mais no raciocínio temos o chamado lucro cessante. Ou seja, o valor que a empresa ganharia se estivesse produzindo e, obviamente, vendendo os produtos, mas que não pode pela máquina parada.
Pegando os 15% da perda acima, só que ao invés de pensar no tempo vamos pensar em dinheiro (R$). Relembrando que estamos sendo simplistas nessa exemplificação, mas o caminho para a justificativa é esse, até porque estamos jogando o valor bem para baixo. Quer ver? E se o problema na máquina tivesse causado um acidente, quanto isso custaria? Tratar o acidentado, colocar outra pessoa no lugar, etc. Isso se não for fatal, aí os problemas são ainda maiores.
Não te convenci ainda? Pense então se tiver que ser feito um recall. Qual seria o custo das substituições dos produtos? E quanto se perdeu na imagem arranhada da empresa? Empresas na bolsa de valores conseguem identificar rapidinho com a queda do valor das ações.
Afinal, quanto se gasta de tempo e dinheiro na ACR?
Resumidamente, os custos são relativos as horas das pessoas envolvidas em identificar o problema, coletar dados, encontrar a causa raiz, dar o devido tratamento e verificar a eficácia. Pode-se ainda somar a esse HH, horas de treinamento e de sistemas.
Exemplo da perda de 15% da máquina: Custo da oportunidade
Digamos que o sistema seja capaz de produzir 1.000 toneladas por ano. Porém, estamos produzindo apenas 850 toneladas por ano, então a oportunidade está na diferença (150 toneladas).
Sendo a margem de R$ 300,00 por tonelada, a oportunidade financeira de 150 toneladas x R$ 300 = R$ 45.000,00.
Pensando nas horas das pessoas capacitadas para resolver problema, temos um valor empregado para a ACR, conforme o desmembramento nas colunas abaixo. Pois, a pessoa recebe um salário, que arredondando, para e empresa ele custaria praticamente o dobro incluindo impostos e benefícios. Logo, conseguimos definir o custo por hora dessa pessoa. Supondo as horas empregadas para resolver o problema em cada fase da ACR conseguimos quantificar o valor de cada recurso. Somando os valores teremos o custo total da ACR, conforme a tabela abaixo:
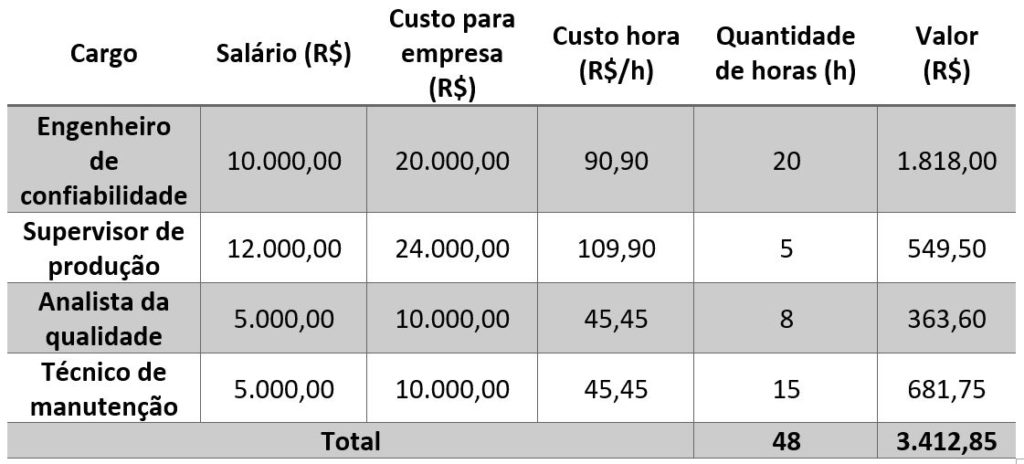
Visando facilitar o cálculo digamos que a equipe tenha recebido um treinamento no valor de R$ 1.587,15. Dessa forma o custo total da ACR fica assim: ACR = HH + treinamento = R$ 3.412,85 + R$ 1.587,15 = R$ 5.000,00
Afinal quanto se ganha com a ACR?
Vamos calcular alguns dos indicadores mais utilizados no mercado para análise do investimento:
ROI = Retorno sobre o investimento
ROI = (Custo da oportunidade – Custo do investimento) / Custo do investimento
ROI = (45.000 – 5.000) / 5.000 = 8
Ou seja, para cada real investido, temos um retorno oito vezes maior!
PAYBACK = Calcula o número de períodos que a empresa leva para recuperar o seu investimento.
PAYBACK = (Custo do investimento / Custo da oportunidade) x 12 meses
PAYBACK = 5.000,00 / 45.000,00 = 0,11
PAYBACK = 0,11 x 12 meses = 1,33 mês = 40 dias
Nessa perspectiva, estaríamos recuperando o investimento em 40 dias!
Representação gráfica do investimento
Custo inicial total = Custo da oportunidade + Custo do investimento
Custo inicial total = R$ 45.000,00 + R$ 5.000,00 = R$ 50.000,00
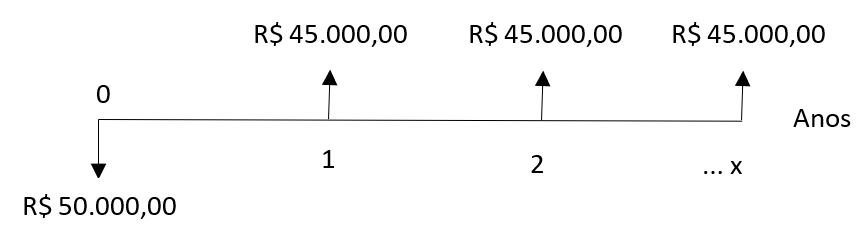
No momento zero tem-se o investimento total, porém, nos anos seguintes entraria no caixa da empresa o valor cheio da melhoria implementada.
Concluindo
Um estudo da Efficient Plant, diz o seguinte: “Average ROIs for RCA range between 600 and 1000 percent”. Ou seja, ROIs médios para ACR variam entre 600 e 1000%. Aqui no nosso exemplo encontramos um valor intermediário de ROI, que ficou em 800%. Como também abordamos a questão do tempo ligado a finanças, encontramos o PAYBACK de 40 dias. Ou seja, todo o esforço para eliminar o problema obteve um retorno de oito vezes em pouco mais de um mês!
Aproveitamos para representar graficamente como ficou nossa simulação do investimento, com o valor no momento inicial de R$ 50.000,00, porém, ano após ano ao eliminar a perda de 15% representou um recebimento a valor presente de R$ 45.000,00.
Reforçando que esse cálculo foi tão somente sobre a ACR, e que normalmente apresenta valores na prática desta simulação. Entretanto, se houver mais custos, eles devem ser adicionados. A ACR exigirá um pouco de educação e algum software para ajudar a organizar o esforço.
Conforme Crosby (1994), “qualidade não custa, mas é, sim, um investimento com retorno assegurado. Na verdade, o que custa e causa vultosos prejuízos às empresas é a “não qualidade”, […]”. Faça o seu cálculo real e surpreenda a direção com o valor (qualitativo e quantitativo) que a ACR poderá trazer para o seu dia a dia. Pois, a resolução do problema em uma área pode ser utilizada em outra área, em outra unidade. Parte importante deste processo está também no aprendizado organizacional. Embora mais difícil de calcular, o seu valor é cada vez mais imprescindível para as empresas.
Também precisamos alertar que o processo de ACR não precisa ser disparado para qualquer problema. A empresa deve estabelecer quando vale a pena. Querendo saber mais sobre esse assunto clique aqui.
Por essas razões é que temos a convicção que realizar ACR não é desperdiçar nem tempo nem dinheiro, mas promover uma cultura investigativa que permita uma melhor utilização destes preciosos recursos. Saiba mais clicando aqui.
Agora que você já sabe o quanto impressionante pode ser a utilização dos métodos de ACR, conte comigo nessa jornada 🙂
Referências
CROSBY, Phillip B. Qualidade é investimento. 6. ed. Rio de Janeiro : José Olympio, 1994.
Efficient Plant https://www.efficientplantmag.com/2002/05/justifying-root-cause-analysis/, acessado em 17/01/19.
UBEROI, R.S.; GUPTA, U.; SIBAL, A. Root Cause Analysis in Healthcare. Apollo Medicine, Vol.1, 2004, 60-63.
ROONEY, J.J. & HEWEL, L.N.V.(2004), Root cause analysis for beginners. Quality Progress.
Imagem da capa: https://www.ukconstructionmedia.co.uk/wp-content/uploads/balancing-cash-and-and-time-251×300.png.
Demais imagens endereço eletrônico clicando na mesma ou próprias da Télios.