Você deseja melhorar continuamente, mas tem dúvida qual a metodologia utilizar? Este post busca simplificar a sopa de letrinhas dos mais utilizados métodos de melhoria contínua (kaizen) e resolução de problemas.
Kaizen (Melhoria Contínua)
Kaizen é a prática da melhoria contínua. Tomou corpo no Japão com o livro Kaizen: The Key to Japan’s Competitive Success em 1986, de Masaaki Imai. Ele se baseia em uma série de princípios:
- eliminação de desperdícios.
- orientação à processos.
- dados e fatos.
- atenção deve estar no local onde o valor é criado.
- trabalho em equipe.
- realizar ações para conter e corrigir as causas bases dos problemas.
Inicialmente vamos considerar o conceito de método como sendo o meio para chegar a um fim, pela observação sistemática de fatos, seguido da realização de experiências, das deduções lógicas e da comprovação científica dos resultados obtidos.
Nesse ponto, temos como fim a melhoria contínua – kaizen, que segundo a ISO 9001:2015 “10.3 Melhoria contínua: A organização deve melhorar continuamente a adequação, suficiência e eficácia do sistema de gestão da qualidade.”
Por quê promover a melhoria contínua?
Seja para atentar e comprovar aos requisitos de normas, ou pelos mais nobres motivos de kaizen como:
- melhoria na qualidade;
- redução de custos;
- aumento na satisfação do cliente;
- mais segurança;
- redução de desperdício na empresa;
- aumento de produtividade;
- compartilhamento do conhecimento;
- maior confiabilidade das máquinas/equipamentos.
Caracterizando os métodos
No quadro a seguir foram elencados os métodos mais usuais lado a lado, partindo do pai de todos, o PDCA. Sim, basicamente cada método segue um desdobramento do ciclo de Deming, como é possível identificar, todos tem quatro etapas, mas com algumas variações de passos entre eles.
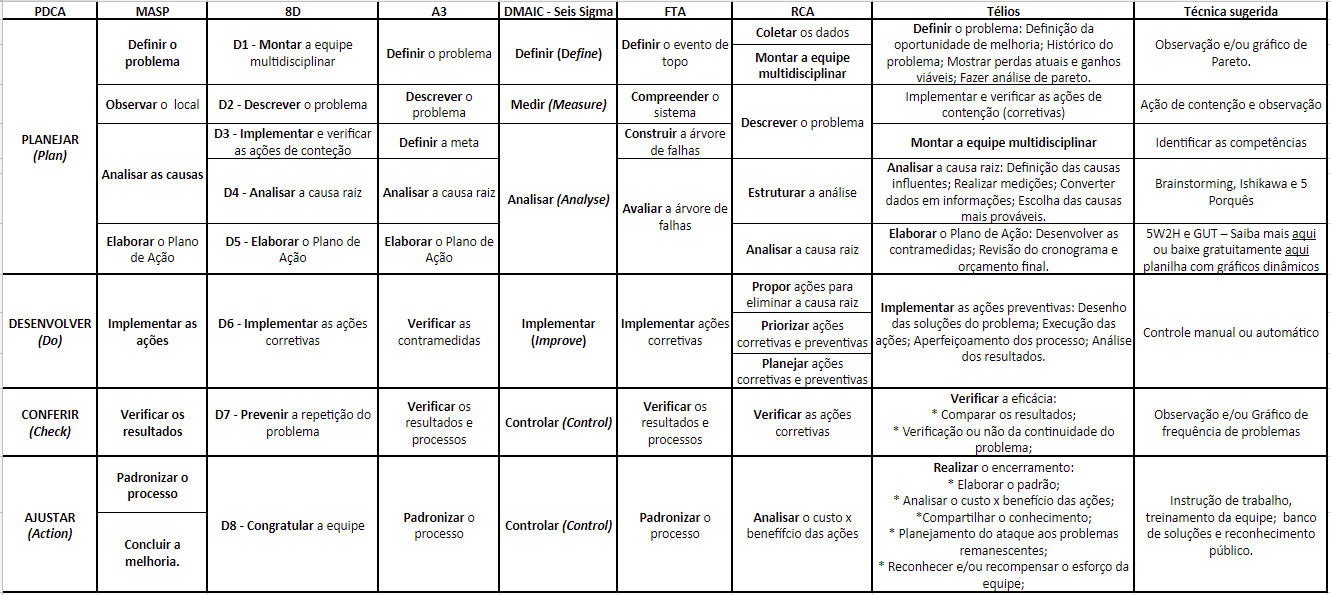
Certamente aqui todos estão cheios de problemas e por isso em busca da melhoria contínua. Então, para que o resultado não seja uma “pioria”, faz-se necessário ter um método estruturado. O que não significa que tenha que ser complexo, ou para “inglês ver”. A forma de trabalho deve estar alinhada com a cultura organizacional. Também considere natural que este método seja aperfeiçoado à medida que a equipe vai ganhando experiência.
Como já dizia Einstein, a formulação de um problema é a parte mais essencial na solução. Então é consenso entre os métodos que o principal ponto para solução de problemas é a identificação de sua(s) causa(s). É sabido também que temos que escolher qual problema, e qual o momento de atacá-lo. Caso necessite de inspiração para isso leia o post “6 dicas de quando apertar o gatilho para acertar a causa raiz do problema na mosca”, onde exploramos o que pode disparar um processo de Análise de Causa Raiz (ACR).
Desvendando a sopa de letrinhas do Kaizen
PDCA: Também conhecido como ciclo de Deming ou Shewhart, o método PDCA busca a melhoria contínua de produtos e processos, identificando as causas de seus problemas e implementando soluções para os mesmos. Graficamente representado pelo círculo em suas quatro fases, entende-se que o ciclo possa ser repetido quantas vezes for necessário sem um fim pré-determinado, sendo essa a base da filosofia do melhoramento contínuo inclusive para os demais métodos a seguir.
8D: A metodologia das oito disciplinas foi melhorada pela Ford Motor Company nos anos 80, visandoa identificação, correção e eliminação da repetição de problemas de produtos e processos.
A3: Método desenvolvido pela Toyota Motor Corporation que estabelece uma estrutura para propor soluções para os problemas, fornecer relatórios da situação de projetos em andamento e relatar as atividades de coleta de informações.
DMAIC: Metodologia para redução de defeitos do programa Seis Sigma, o DMAIC é um ciclo de desenvolvimento, caracterizado pela utilização intensiva de técnicas estatísticas, utilizado em projetos de aumento de produtividade, redução de custos, melhoria de processos administrativos, dentre outras aplicações.
FTA: Método da Análise da Árvore de Falhas, traduzido do inglês “Fault Tree Analysis – FTA” foi desenvolvido por volta de 1960, por W.A. Watson, da empresa Bell Laboratories e aperfeiçoada pela Boeing Corporation. Sua metodologia é dedutiva e estruturada em termos de eventos, ao invés de componentes, que tem por objetivo melhorar a confiabilidade em geral de produtos e de processos por meio da relação lógica entre falhas primárias e falha final do produto buscando assim a resolução de problemas.
MASP: É uma abreviatura usada para o Método de Análise e Soluções de Problemas é a denominação que o QC-Story, método de solução de problemas de origem japonesa, foi atribuída no Brasil. Trata-se de um roteiro para manter, controlar e aperfeiçoar a qualidade de produtos e processos passando pela verificação do resultado da solução e, finalmente, geração e disseminação de aprendizado decorrido de sua aplicação.kaizen
RCA: A Análise de Causa Raiz (ACR) ou traduzido do inglês “Root Cause Analysis – RCA” é um método para o uso investigativo na identificação da causa raiz de um evento, o qual pode ser com segurança, saúde, meio ambiente, qualidade e impactos na produção.
Télios: Embasado nas diversas metodologias, porém desenhado para atingir resultados expressivos rapidamente e facilitar o trabalho de gestão.
Rigor versus prática
Mesmo que aqui sigamos o rigor científico e metodológico nas nossas colocações, também ajustamos à nossa realidade prática. Por isso, acreditamos que antes de qualquer estudo, precisamos garantir que o problema não se alastre tomando ações imediatas até que as ações planejadas aconteçam.
Outro ponto importante, é que embora respeitemos muito a forma circular do PDCA, temos da literatura e principalmente das técnicas de métodos ágeis, que esses processos criativos não são obrigatoriamente lineares, ou seja, podemos retornar a pontos anteriores sempre que necessário. Por exemplo, problemas menores não precisam necessariamente de todas as etapas para serem solucionados. Sugerimos que ao menos eles sejam registrados. Se voltarem a ocorrer e tornarem-se mais graves, esse histórico torna mais fácil e assertiva a solução. Com isso, ganha-se tempo por não esgotar todas as possibilidades antes de seguir em frente, e ao mesmo tempo proporciona maior flexibilidade.
Execute e compartilhe!
Nesse sentido, independentemente do método estar 100% dentro da literatura, o mais importante a fazer é compartilhar o conhecimento para sair do ciclo vicioso dos problemas e entrar na espiral virtuosa das soluções. Temos um norte, mas a situação vai indicar a melhor trilha a ser seguida.
Se você procura um meio mais fácil e eficiente para ser “Hoje melhor do que ontem, e amanhã melhor do que hoje”, utilize gratuitamente a plataforma Télios. Para isso basta realizar o rápido cadastro aqui e sair utilizando.
E você, qual método utiliza? Não perca o detalhamento dos métodos nos próximos post e responda o formulário neste link que te manteremos atualizados com conteúdos ricos sobre melhoria contínua.
Sobre o autor
Carlo Rossano Manica é Engenheiro de Produção, Msc Inovação UFRGS, +20 anos de experiência profissional e acadêmica em tecnologia e inovação, gestão de projetos, produção e manutenção, além de três especializações em negócios. Atualmente é CEO na Télios, professor de engenharia de produção no IPA.
Referências bibliográficas
BAPTISTA A. J. – A importância da análise de causa raiz (root cause analysis) na melhoria do desempenho da manutenção industrial http://www.abraman.org.br/arquivos/191/191.pdf
CAMPOS, Vicente Falconi. TQC: Controle da Qualidade Total (no estilo japonês). 8. ed. Belo Horizonte: Bloch Editora, 2004.
CARVALHO, Marly Monteiro de; ROTONDARO, Roberto. Modelo seis sigma. In: Gestão da qualidade: teoria e casos. 2. ed. rev. e ampl.[S.l: s.n.], p. 430 , 2012
DOWNING, M. W. Root-Cause Failure Analysis: Maintenance and Reliability Best Practice. Plant Engineering. Dupont, 2004.
LAFRAIA, J. R. B.; Manual de Confiabilidade, Mantenabilidade e Disponibilidade. Rio de Janeiro: Qualitymark, 2001.
http://www.cs.ucf.edu/~hlugo/cop4331/ericson-fta-tutorial.pdf
Oliveira H.F. et al – Matriz a3–uma abordagem acerca das diferentes complexidades dos problemas, Revista Latino-Americana de Inovação e Engenharia de Produção.
SHOOK, J. Gerenciando para o aprendizado: usando um processo de gerenciamento A3 para resolver problemas, promovendo alinhamento, orientar e liderar. São Paulo: Lean Institute Brasil, 2008.
https://www.manutencaoemfoco.com.br/fta-fault-tree-analysis-parte-i/